Driving Innovation with Integrated Engineering Support: From CAD Modelling to CNC Fabrication
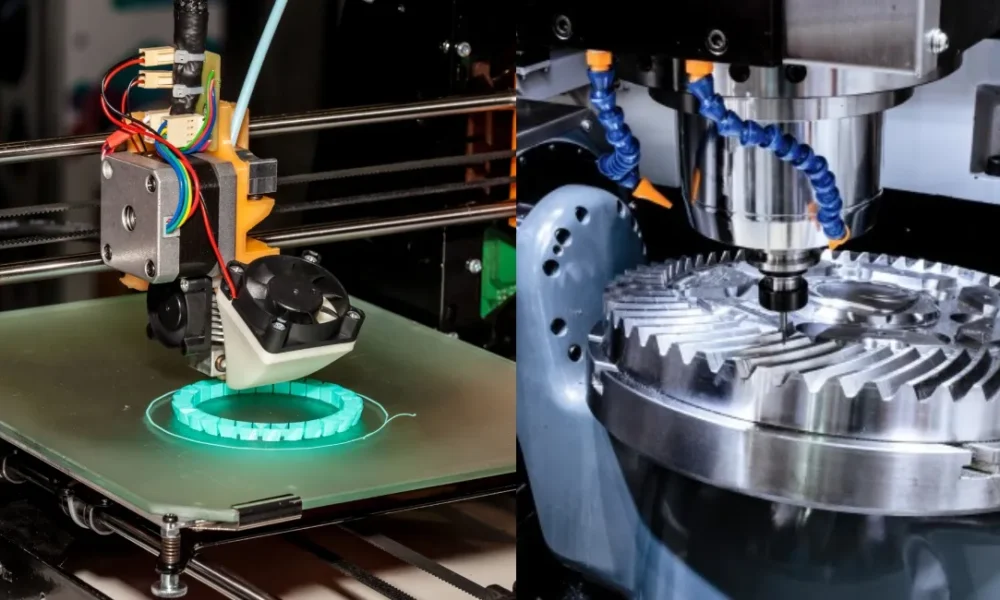
In today’s fast-paced industrial landscape, companies are under immense pressure to bring products to market faster, reduce costs, and maintain high standards of quality. Achieving these goals requires a comprehensive approach to product development that merges design innovation with advanced manufacturing techniques. Modern enterprises, whether OEMs or startups, are increasingly turning to cnc programming services, engineering support systems, and digital tools to streamline workflows and enhance product lifecycle management.
This article explores the critical elements of contemporary mechanical engineering and manufacturing design—focusing on CAD modelling, sheet metal design, reverse engineering, CNC fabrication, and Design for Manufacturing (DfM)—and how Engineering Services Outsourcing (ESO) is reshaping traditional development pipelines.
CAD Modelling Services: Building the Foundation
Computer-Aided Design (CAD) modelling is foundational to modern product development. It transforms conceptual sketches or functional ideas into fully realized 3D models that serve as blueprints for subsequent engineering and manufacturing tasks. Beyond geometric accuracy, CAD systems today integrate parametric modeling, version control, and simulation tools, enabling engineers to optimize designs for performance, compliance, and cost.
CAD modelling services are particularly vital during the early phases of concept development. Engineers can evaluate component fitment, simulate kinematics, and even assess thermal or stress behavior using integrated tools. The result is a reduced risk of late-stage design changes, which can be costly both in time and resources.
This digital backbone not only supports design intent but also facilitates seamless collaboration among distributed teams, a key advantage in Engineering Services Outsourcing environments.
Sheet Metal Design: Precision Meets Practicality
Sheet metal remains one of the most versatile and widely used materials in industrial design. From consumer electronics enclosures to automotive brackets and aerospace panels, effective sheet metal design can significantly impact product durability, weight, and manufacturing costs.
Expertise in sheet metal design extends beyond drafting flat patterns. Engineers must understand material properties, bend allowances, reliefs, and tolerancing, especially when designing for CNC sheet metal fabrication. Specialized CAD tools for sheet metal allow real-time flattening, automatic bend calculations, and manufacturing validation.
Furthermore, successful sheet metal components must be optimized for assembly processes such as welding, riveting, or fastening. Incorporating Design for Assembly (DfA) principles alongside DfM strategies ensures manufacturability without compromising functionality or aesthetics.
Reverse Engineering Support: Bridging Legacy and Innovation
Reverse engineering has become an indispensable part of the modern engineering toolkit. Whether the objective is to replicate obsolete components, analyze competitor products, or digitize hand-built prototypes, reverse engineering provides a critical pathway to knowledge recovery and innovation.
The process typically begins with 3D scanning or CMM inspection of the physical part, followed by point cloud processing, surface reconstruction, and CAD modelling. Reverse engineering support requires not only technical expertise but also a strong understanding of the original design intent, materials, and performance conditions.
For manufacturers maintaining legacy equipment or systems with undocumented modifications, reverse engineering becomes essential for repair, upgrade, and documentation purposes. Coupled with modern mechanical engineering design services, it enables organizations to evolve aging products to current standards.
CNC Sheet Metal Fabrication: From Digital to Physical
Once designs are finalized, fabrication begins—and this is where CNC machining and sheet metal processing come into play. CNC sheet metal fabrication combines the precision of computer-controlled machinery with the adaptability of sheet metal processes like laser cutting, punching, bending, and forming.
High-quality CNC programming services ensure that part geometries are accurately translated into toolpaths, taking into account material behavior, machine kinematics, and process constraints. Skilled programmers optimize tool usage, minimize cycle times, and reduce material waste, thereby increasing both productivity and profitability.
CNC fabrication also allows rapid prototyping and short-run production, giving engineering teams the flexibility to validate designs quickly. Tolerances can be tightly controlled, and repeatability is high—both crucial for sectors like aerospace, automotive, and medical device manufacturing.
Concept Development: Turning Ideas into Engineering Reality
The earliest stage of any product development process begins with concept development—transforming an abstract idea into a viable engineering solution. This involves market research, feasibility studies, preliminary sketches, and multiple rounds of concept iteration. At this stage, engineers must balance innovation with constraints such as cost, manufacturability, and regulatory compliance.
Tools like 3D modeling, simulation, and virtual prototyping play a crucial role in refining concepts before physical prototypes are produced. Additionally, collaborative input from industrial designers, mechanical engineers, and manufacturing specialists is essential to align functionality, aesthetics, and production feasibility.
In the context of Engineering Services Outsourcing, concept development benefits from multi-disciplinary talent pools, time zone leverage, and access to specialized technologies without incurring the overhead of full-time in-house teams.
Design for Manufacturing (DfM): Ensuring Feasibility and Cost-Efficiency
A brilliant design that cannot be manufactured efficiently is of little commercial value. Design for Manufacturing (DfM) ensures that products are optimized for real-world production processes—be it CNC machining, injection molding, casting, or additive manufacturing.
DfM involves evaluating a design for process compatibility, tolerance stack-ups, material usage, and assembly complexity. Common goals include minimizing part count, reducing material waste, and simplifying jigs or fixtures. DfM reviews often take place during design validation and prototype phases but are most effective when integrated early in the design cycle.
The feedback loop between design engineers and manufacturing experts enables iterative improvements and reduces time-to-market. With DfM, rework and scrap rates decline significantly, leading to higher yields and lower unit costs—critical metrics in competitive industrial environments.
Integrating Engineering Services for Scalable Growth
As products become more complex and lifecycles shorten, many companies are turning to mechanical engineering design services providers to augment internal capabilities. This trend toward Engineering Services Outsourcing is driven by the need to access domain expertise, increase design bandwidth, and manage costs effectively.
Outsourcing partners can provide end-to-end support, from CAD modelling and simulation to prototyping and production documentation. With cloud-based collaboration platforms and secure data management, geographical barriers are no longer a hindrance. Engineering services partners also bring cross-industry knowledge, which can spur innovation by applying best practices from adjacent domains.
Additionally, integrated partnerships help ensure design continuity, allowing rapid iterations based on field data or changing customer requirements. Whether it’s updating a design to meet new compliance standards or re-engineering a product for cost reduction, outsourced engineering teams offer the flexibility needed in today’s market dynamics.
Conclusion
The synergy between design and manufacturing has never been more critical. Engineering teams today must navigate the intersection of innovation, practicality, and scalability—leveraging digital tools, expert knowledge, and smart manufacturing techniques to remain competitive.
Whether you’re utilizing advanced cnc programming services, engaging in Engineering Services Outsourcing, or seeking cutting-edge mechanical engineering design services, a well-structured development pipeline is key to success. From concept to CAD, and from prototype to production, every stage of the engineering process benefits from integrated thinking, rigorous validation, and a commitment to manufacturing excellence.
In an era where precision, speed, and adaptability define success, the fusion of design intelligence and production capability is not just advantageous—it’s essential.
Read More From Techbullion